
Fabio Pagliero, CEO of Multitel Pagliero, describes how the company’s supply chain has been organised throughout the years.
A SUPPLY CHAIN IN SHORT
The supply chain refers to the process that brings a product or service to the market: from the flow of raw materials for manufacture to the logistics for ensuring that the purchased goods are correctly distributed to the customer. The term supply chain management (SMC), on the other hand, describes the work of coordination that optimises each link in the supply chain. Present day supply chains, which are certainly more complex than a few years ago, are divided into three main phases that can be broken down into smaller processes:
- procurement: this refers to how, where and when to request the raw materials needed for production
- production: the manufacturing work where the raw materials are used
- distribution: this includes all the operations that lead to the delivery of a given item to the customer, through the organisation of logistics and its operators
Supply chains are becoming more complicated every day in terms of speed, flexibility, precision and efficiency required. New digital technologies with sophisticated data management play a fundamental role in planning, which must predict the demand for a product and then coordinate the links in the supply chain to deliver it. Not only must it forecast and plan demand but also plan supply, production, sales and operational activities.
2012 YEAR OF THE TURNING POINT AT MULTITEL PAGLIERO
As Fabio Pagliero explains to us, “the process of organising the supply chain at Multitel Pagliero began in 2012 when processes that had previously been delegated to third parties were transferred in-house. In practice, for the models of truck-mounted platforms of 30 metres and above – numerically smaller – some activities, particularly for the steel structure and hydraulics, were already carried out internally. Multitel Pagliero, which only employed 200 people at that time, was more like an artisan’s workshop and it was difficult to find external suppliers able to produce one or two large and technically delicate pieces at a time. Pieces that were designed by us in any case”.
The constant increase in demand, in higher quantities for standard production models, was the push we needed to internally reorganise. “This required investments in machinery and production sites, and given that elements such as sheet metal parts, gaskets and valves were made to our design, it made the transition easier. More difficult was finding qualified staff to use the robots, automatic work centres or painting plants. We now had the product; what we needed were people. And this resulted in an increase in staff numbers from 200 to 550 employees”. The organisation of the supply chain therefore supported, followed and stimulated the company’s growth.

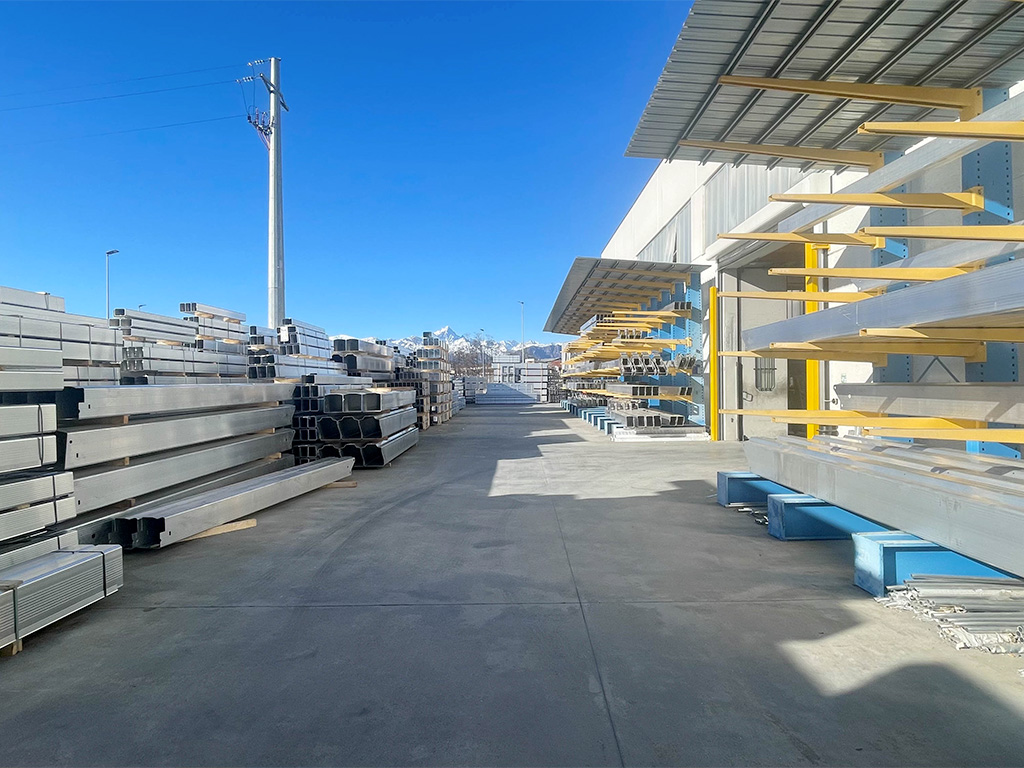
Chronologically, the internal organising of the processes involved:
2013 – aluminium (booms, cages, base frames)
2014 – purchase of vertical automated storage systems
2014/2015 – painting plant which was 50% external
2016/2018 – cylinders with a major investment and people specialised in managing the programming
2017/2018 – electrical systems
2020 – metal structures
In 2021, while design and planning of the machines was handled 100% internally, even production in-house amounted to 95%. The remaining 5% related to trucks, components (valves, batteries, microchips) delegated to very trusted manufacturers, and the raw materials (aluminium and iron). This area is the responsibility of the purchasing department.
“The supply chain”, Fabio Pagliero emphasises, “moves forward independently, department by department. Although I’m in contact with all the managers on a daily basis, meetings are not necessary as the supply chain is well-established and the decision-making chain is short. This allows us to keep less inventory, produce according to orders received and ensure a higher quality of work control. Unlike an external supplier, we are very acutely aware that our truck-mounted platforms are used by people, and so we cannot afford to make any mistakes”. Production independence has required the purchase of machinery able to make the parts designed by the technical department, which would be impossible to ask of a contractor who doesn’t work for us exclusively and does not even have the right facilities to meet demand. “For our part,” Fabio Pagliero points out, “knowing that we produce X number of machines every week, everything is planned. This means that it would not be difficult, if necessary, to add another plant, remodel the supply chain and redirect production”.
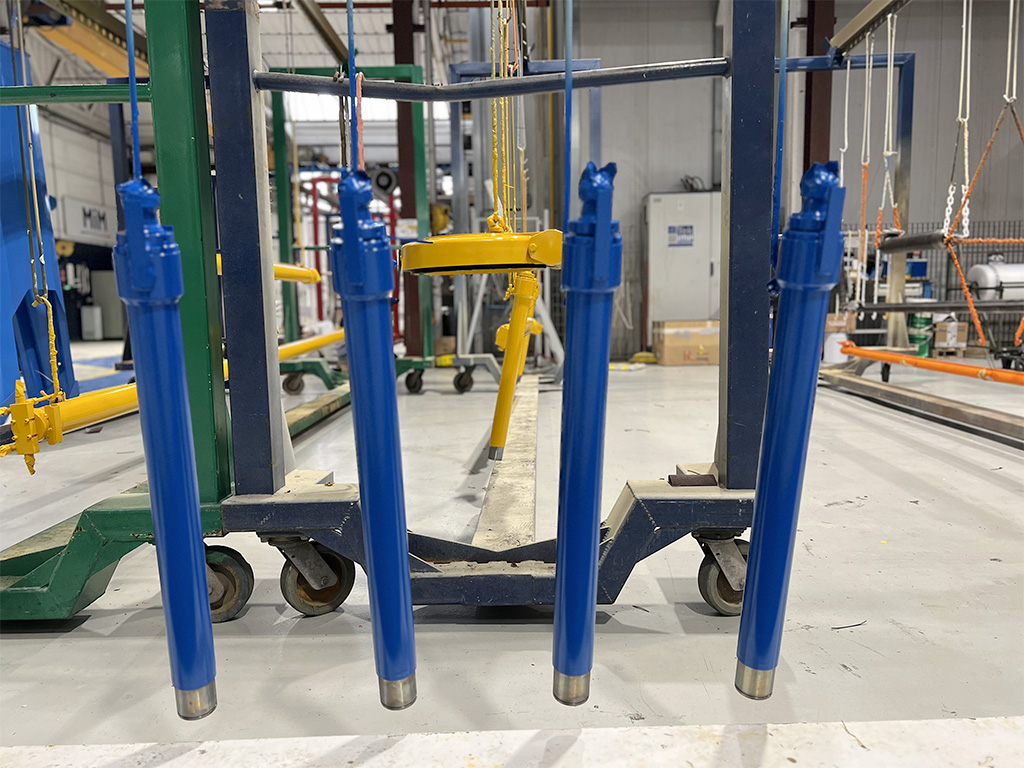
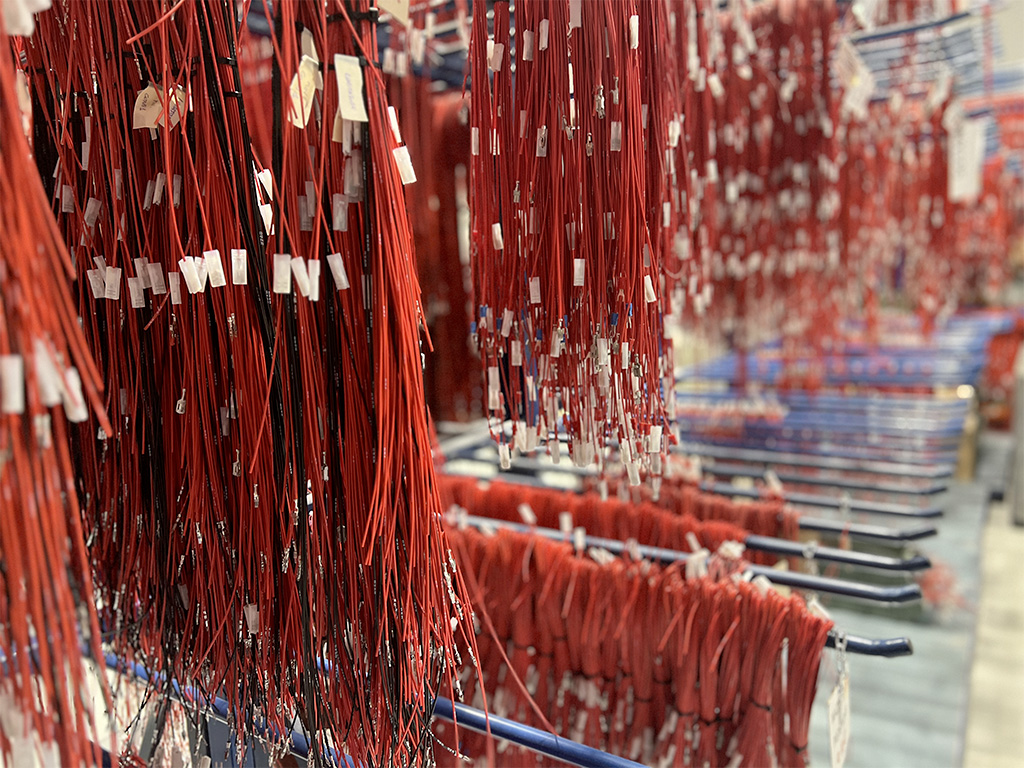
From 2021 to 2023, our organisation, structure and flexibility have allowed us to easily keep up with the surge in demand, which in 2023 saw a peak of 2250 units produced, almost 50 machines per week. It is clear that the staff to manage this type of production must be highly specialised and, since they are not easy to find, they require training from the moment they enter the plant. Those with experience, in addition to broadening their technical knowledge, share it with new resources and thus create a “common language”. This is essential for eight independent high-tech units, with machines operating 16 hours a day, each dedicated to one specific activity: aluminium welding, iron welding, lathe operations, painting, processing of electrical panels. Companies individually capable of generating business, which work without outside influences and from which the elements destined for the assembly unit of the truck-mounted platforms come out. Information technology with Industry 4.0 has made a decisive contribution to data management and continuous monitoring of the production chain, allowing us to coordinate times and meet deliveries.
Could more be done, and better?
“Every activity”, concludes Fabio Pagliero, “can be improved and, at present, the Multitel Pagliero supply chain is almost perfect. If we were to think about bringing another process in-house, I would go for electronics, specifically the electronic boards, which represent the most ambitious project to be achieved”.