Andrea Scaglione holds a degree in mechanical engineering specialising in automation and biomedical engineering. 19 years’ experience in the industry, manager of process technology for the last three years, he clarifies the strategic importance of these processes to Multitel Pagliero’s production growth.
What are “process technologies” and what is their objective?
The combination of machinery, equipment and systems required for manufacturing is known as process technologies. My job is to monitor all departments and try to give them the best technical solutions for the tasks they need to complete. I also assist with installation and start-up, manage maintenance, and ensure that the equipment is kept in good working order until it is decommissioned and replaced.
What does becoming the manager entail?
To fully appreciate the potential, needs, priorities, critical challenges and dangers of each department, service and production process, a manager of process technologies must have as broad a perspective as possible. It means listening to people and engaging with them to generate chances for development. It means being present in every department and looking at the dynamics of production, maintaining relationships of collaboration and trust at all levels. It means building a knowledge network outside the company through which we can always be updated on the technologies of interest to us.
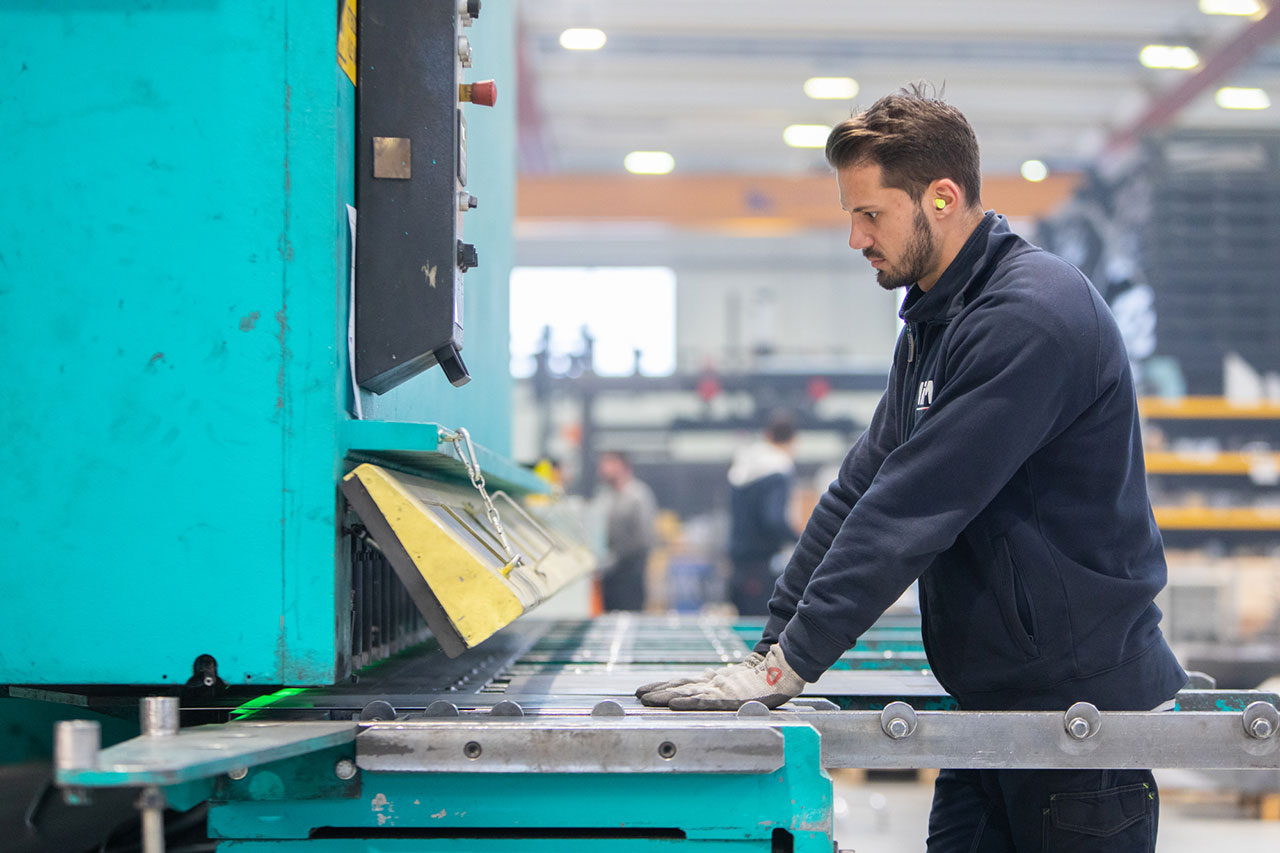

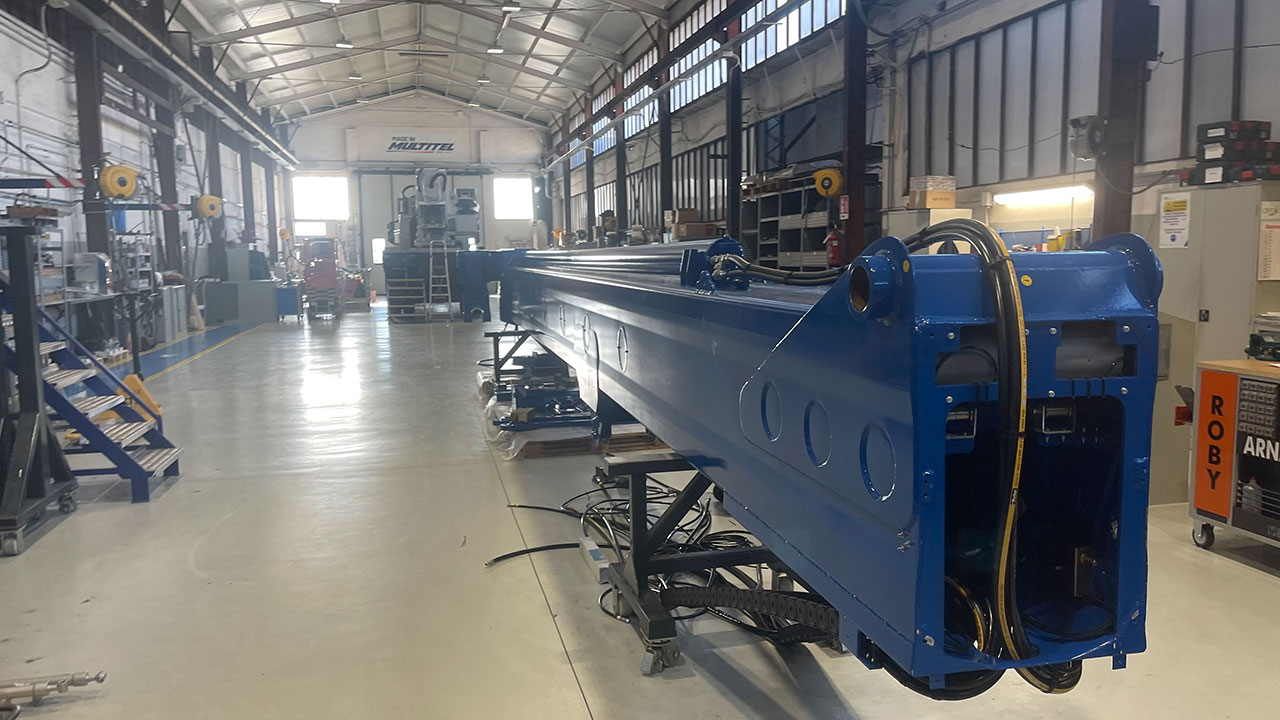
What is the size of the work group?
In addition to me and some external companies with which we have an ongoing working relationship, there are three other internal members:
- Simone who primarily assists me with managing deadlines, paperwork and bureaucratic tasks.
- Michele electrical maintenance worker with experience of being seconded out to install automatic systems.
- Davide mechanical maintenance worker with experience in lathes and machine tools.
To what extent and in how many areas do you intervene?
We get involved with anything that has to do with warehouses (building, general systems, lifting and handling systems), with all workshop machinery and equipment (power tools, control units, benches), and with anything relating to production in general. The degree of intervention must be sufficient to resolve the problems reported, and in situations where we are unable to finish the task, we will get in touch with and assist outside partners and the machinery/system service professionals. My primary areas of responsibility are management and organisation, where I arrange the availability of technicians and the acquisition of materials. But I also like getting my hands dirty and being directly involved in all the action.
What qualities, both personal and professional, are necessary for a process technology manager?
People in this industry deal with owners, managers, and production staff as well as external service professionals and sales representatives from businesses that provide machinery and services. A strong technical foundation is necessary in all fields, particularly in mechanics, electrical engineering and hydraulics, both theoretical and practical. However, the essential experience you acquire on a daily basis is something no one can teach you. Another quality is the ability and intention to take decisions, because in problem solving and project development, there are rarely manuals and procedures. Instead, you assess the situation, consider the input from all parties involved, and decide on the best course of action. Being a motivating leader is the final crucial element.
Which other managers and supervisors do you report to and engage with?
I interact with and report to all the service and production managers. I deal daily with the Production Manager for the numerous “mutual interferences” and with the Security Manager for everything concerning risk mitigation. I also work closely with the IT manager because technology and connectivity are crucial factors. I also regularly interact with the owners, purchasing and administration for expenses and investments, and with marketing to support the most innovative choices.
What is the approach to work at Multitel Pagliero, which has a large number of factories, each of which is “specialised”?
Each production unit is a world in itself: when entering, you can be sure that you will find different references and dynamics, specific machinery and technologies. However, the approach is the same in all the factories because ultimately the goal is the same.
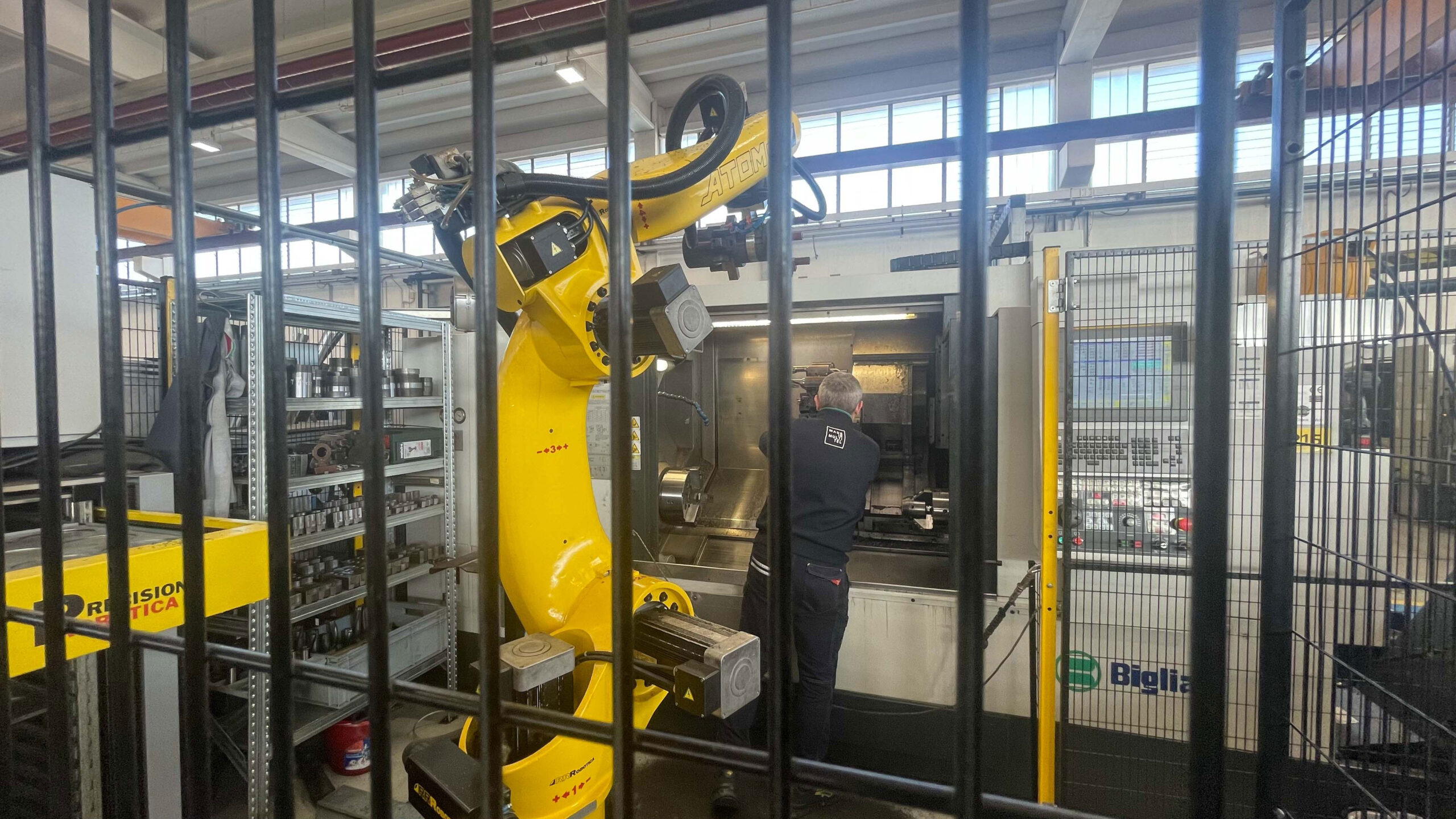
Does the task get simpler or harder as a result of the subdivision?
Given the complexity and variability of the process involved in developing, constructing, and finishing our platforms, subdividing the processes makes sense. Every warehouse has its own specific machinery and systems, as well as staff that have been trained and have a lot of experience managing them.
The complication is instead due to the fact that each production unit is separate from the others and this means that the spaces of each area are constrained and that all the general systems must be repeated for each unit.
Should the process technology in this instance strike a balance between the overall production goals and those of the individual unit?
Each production unit contains one or more departments. Regardless of their location, departments must have plants, machines and equipment sized appropriately for their activity, ideally with some spare capacity. The balance of resources based on the production mix is then defined by the Production Management.
How and to what extent are processes affected by technological innovation?
Technological innovation is a fundamental factor for business growth. Innovation must put the company in a position to produce more, of higher quality and in faster turnaround times and at cheaper costs. Keeping up with the competition and perhaps even gaining some market share requires investing in the right cutting-edge technologies. My attention and participation are focused on the production system to ensure this situation is maintained, as Multitel Pagliero has long been recognised for its technological prowess.
Can you give two examples introduced in the past year?
We have chosen to concentrate on a variety of items, and I can provide two instances of technological innovation linked to the production process of large-scale machines.
The launch of a new laser cutting system featuring a large bench and an adjustable cutting head is one instance. This substantial investment has made it possible to group together in a single machine several activities that were previously performed in a less effective, less precise, and more costly manner. More specifically, in order to produce the sheet metal strips used to make the booms of large equipment, it used to be necessary to shear the sheets several times, load the semi-finished products onto a bench for plasma cutting in order to create openings and cut specific profiles, and then manually finish the cut profiles in order to remove any processing residue and create any bevels in order to get them ready for welding. Costs, movements, and times. The new machine does everything in a single step, with a level of finish and precision that was not previously possible, and in a substantially shorter amount of time. It also permits an increase in the maximum dimensions of the booms.
A new robotic cell for welding frames and base blocks is the second instance of recent technological innovation. This large-scale system consists of two stations with differentiated positioners for rotating the frames and for rotating and tilting the base blocks. An articulated robot moves back and forth between the two stations, welding each joint according to a specific welding cycle. The efficient search for welding joints using an optical sensor and, soon, the testing of an innovative remote programming method based on the 3D design of the subgroups to be manufactured further improve this approach. In this instance, the technological improvement allows for the automation of a process that was previously carried out manually on support benches or trestles, producing long welded sections and complex movements of the subgroups.
Process technology affects how employees operate. How are changes communicated and shared. How do people react to them? How long does it take for them to become fluid/automatic?
During the development and budgeting stage, operators and department heads are consulted as much as possible regarding technological innovations. They are the ones who are most familiar with the limitations of the starting process and know what the expected quality targets are. Technological innovation is not an end in itself, but also aims to improve working conditions and allows operators to grow professionally. Accompanying each innovation, it is important to identify the appropriate person to oversee the start-up, optimisation and management. It is a natural process that requires a little support and adequate training.
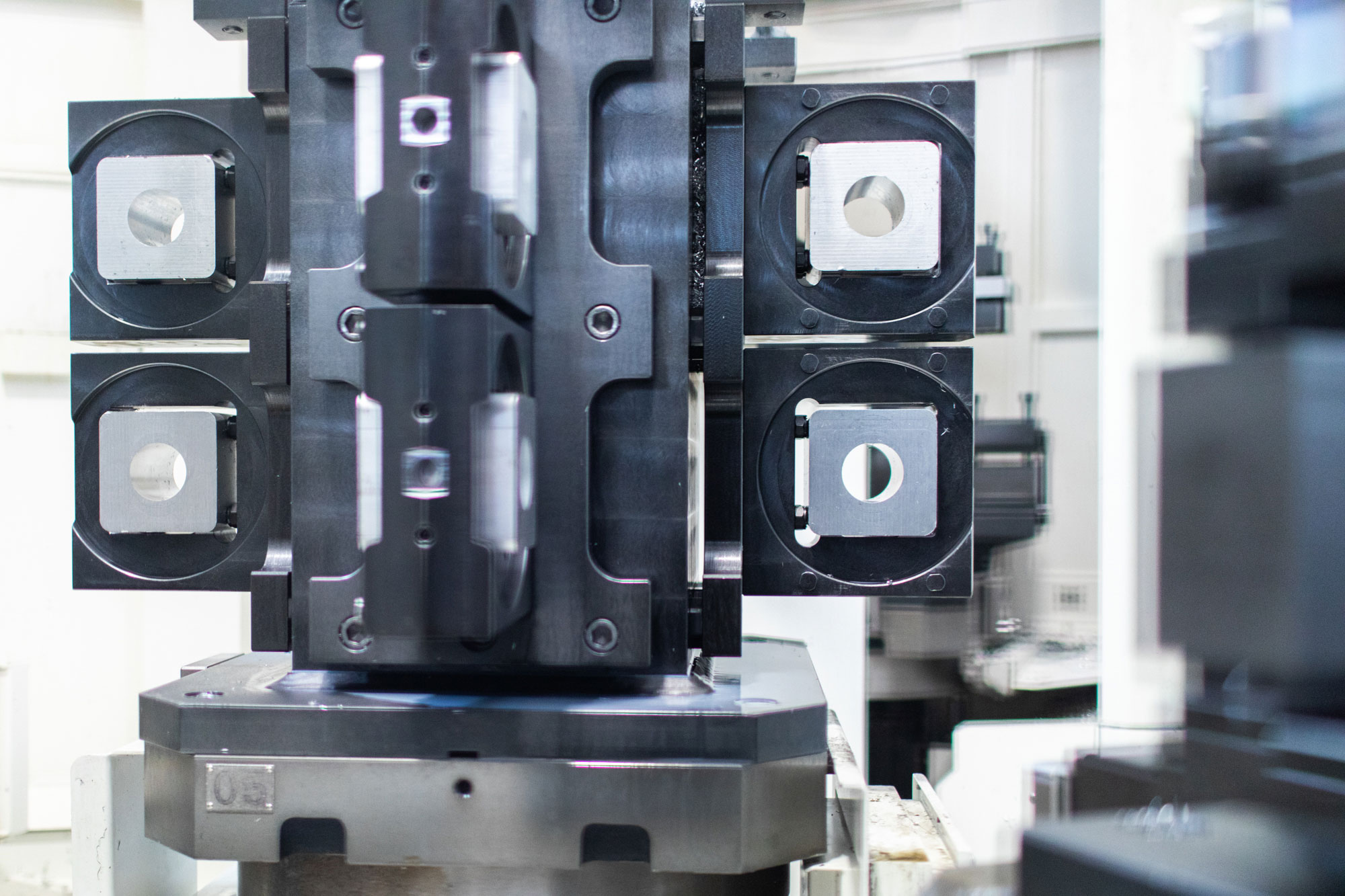
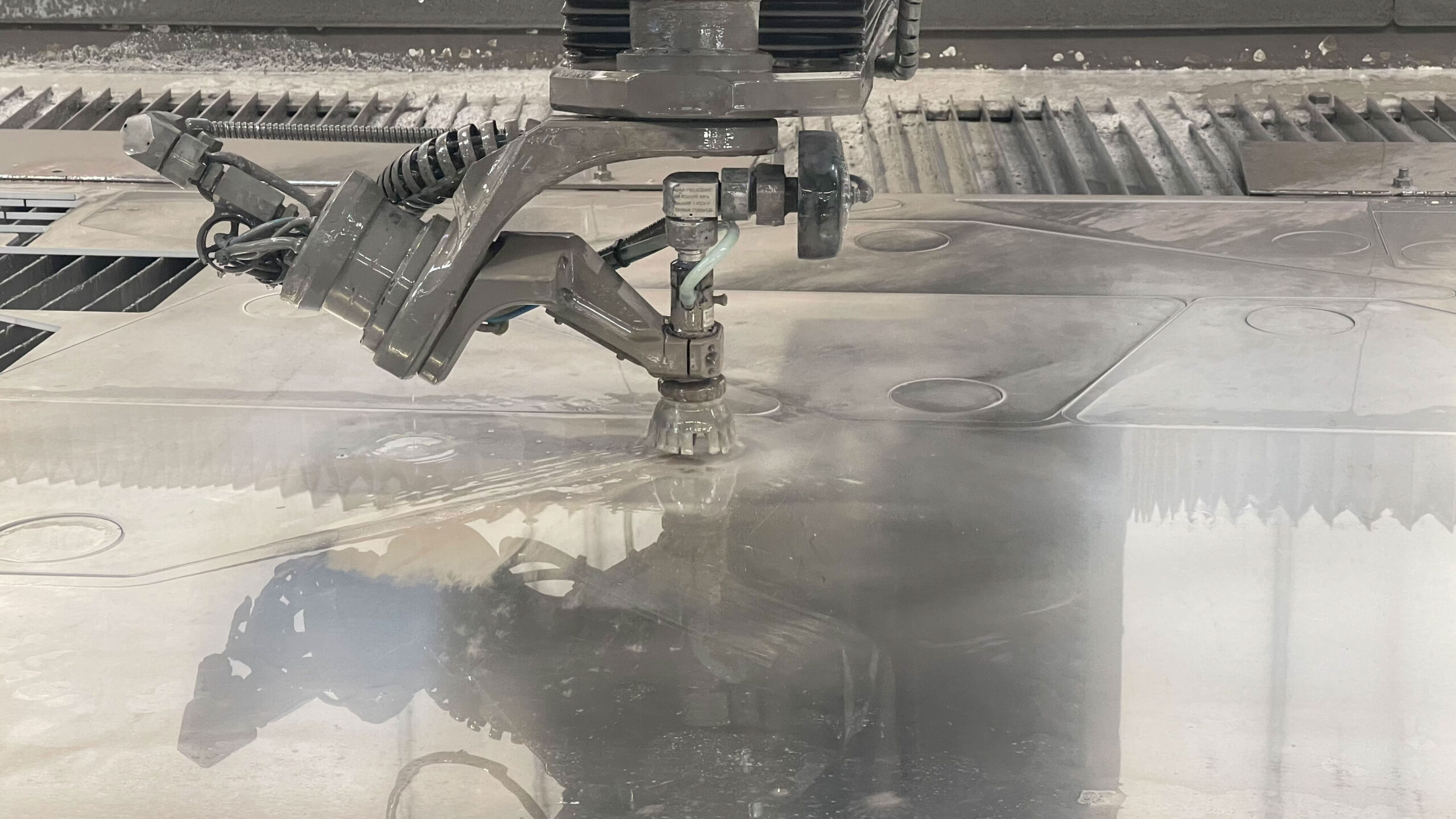
How and to what extent does process technology impact on staff safety?
Technological innovation is frequently brought about specifically to address circumstances that have previously proved dangerous. More broadly, process technologies and maintenance need to concentrate on all the critical situations identified in the company; at times, just providing the right equipment for an activity can have a big impact on operating safely, as can small precautions and improvements. One of our responsibilities is also to restore and confirm the machine’s defences. A number of contracts for the management and safety inspection of all equipment and tools used for handling and lifting, electrical and heating systems, walkways, and escape routes also ensure the safety of the workforce.
Productivity, and the number of staff, have grown over the last three years. I imagine that in order to manage and accomplish these results, the work group’s contribution was essential.
I firmly believe that, over the past three years, we have made a very positive contribution. I am sure that significant progress has been made, particularly in the area of managing the most critical production processes – we have learnt how to manage them and control their operating drifts – in conjunction with both internal and external collaborators. The fact that many of the machines are relatively new meant that an organised maintenance and control system had not yet been put in place. We immediately began to organise the spare parts to keep available, to plan targeted interventions to address the primary causes of machine downtime and to activate assistance contracts. We have reinforced the processes in which we were weakest and we take all reasonable precautions to keep the most at-risk situations under control; we are working to propose solutions that will allow us to further strengthen the critical processes in the upcoming years.
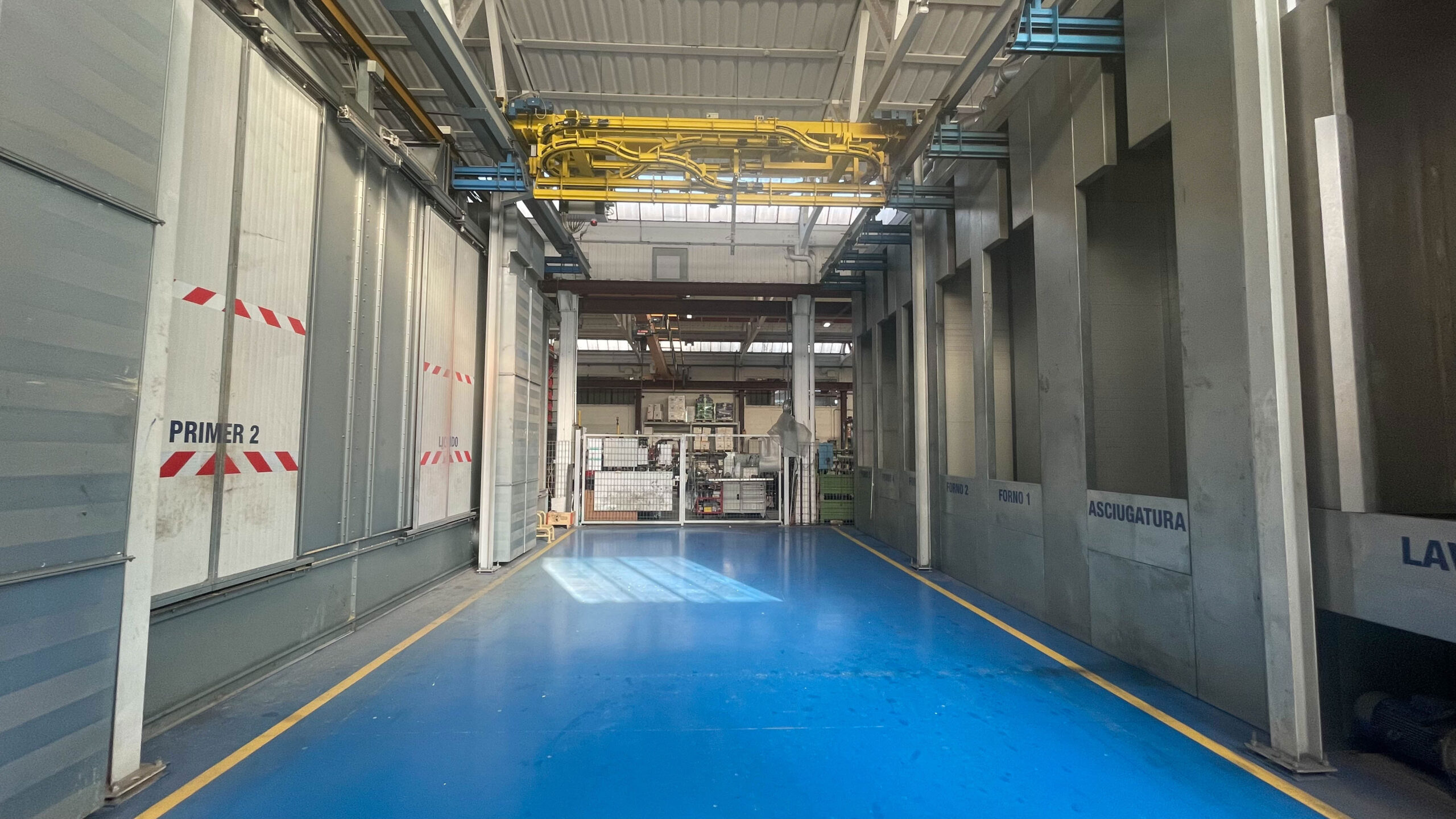
Do you think the processes will change over the next 12 months?
I anticipate significant changes to the Manta2 washing and pickling process, the semi-automatic boom welding system at Manta7 being retrofitted, and the addition of some strategic machinery to the machine tool sector throughout the next 12 months.
What objectives need to be achieved next?
In addition to what has already been mentioned, the goals include improving the service by developing skills rather than hiring more employees, expanding our network of contacts, and working with technicians able to actively and promptly support us.
You participated in the Multitel factory image restyling project last year, which was rather out of the ordinary for you. How did you feel about this experience?
The Multitel Pagliero image restyling experience was a useful opportunity to introduce the departments to the MiM ethos while also giving the common areas of each warehouse a thorough cleaning, a little colour and a freshen up. This is an ongoing process that has encompassed the construction of the new canteen and also involved the external branches.

Process Technology Manager
I have been part of Multitel for almost three years and, because of my role, I work with all the departments. Throughout my professional experience, I have encountered prosperous Piedmont companies that, despite varying in size and organisation, manage to distinguish themselves via their entrepreneurial spirit and efficient work ethic. I’ve discovered that the top businesses in our territory, regardless of their industry, share healthy aspirations and a strong desire to believe in their product, as well as a strong brand identity that encourages employee identification and teamwork in addition to individual initiative. These elements, in my opinion, are also strongly ingrained in Multitel. We understand that we are the industry standard, and it is our responsibility to make every effort to maintain this status.