
Fabio Pagliero, administrateur délégué de Multitel Pagliero, explique comment a été organisée, au fil des années, la chaîne logistique de l’entreprise.
QU’EST-CE QUE LA CHAINE LOGISTIQUE: UNA SYNTHÈSE.
Le terme « chaîne logistique » ou « chaîne d’approvisionnement » (en anglais, supply chain) indique le processus par lequel un produit ou un service arrive sur le marché : depuis le flux de matières premières destinées à la production jusqu’à la logistique de distribution, qui se charge de faire arriver le bien au client qui l’a acheté. Quant à l’expression « gestion de la chaîne logistique » (en anglais, supply chain management – SCM), elle concerne des activités de coordination visant à optimiser les différents anneaux de la chaîne d’approvisionnement. Certainement plus complexe que les filières existant il y a quelques années encore, la chaîne logistique s’articule en trois grandes phases principales, elles-mêmes décomposables en différents processus:
- Logistique des achats: en d’autres termes, comment, où et quand demander les matières premières nécessaires pour réaliser la production.
- Logistique de production: c’est l’activité de fabrication proprement dite, dans le cadre de laquelle on utilise les matières premières.
- Logistique de distribution: elle comprend toutes les opérations qui, par le biais de l’organisation de la logistique et de ses acteurs, mènent à la livraison d’un bien donné au client.
Les chaînes d’approvisionnement deviennent chaque jour plus complexes, plus exigeantes en termes de rapidité, flexibilité, précision et efficience. Et les nouvelles technologies numériques, avec leur gestion sophistiquée des données, jouent un rôle fondamental dans la planification. Celle-ci doit prévoir la demande d’un produit et ensuite coordonner les anneaux de la chaîne d’approvisionnement pour le livrer. Outre la prévision et la planification de la demande, elle inclut aussi la planification de la fourniture, de la production, des ventes et des activités opérationnelles.
2012 – UN TOURNANT POUR MULTITEL PAGLIERO
Comme nous l’a expliqué Fabio Pagliero, «le processus d’organisation de la chaîne logistique dans notre entreprise a commencé en 2012 avec le transfert dans notre usine de certains types de travaux précédemment confiés à des tiers. En réalité, pour des modèles de nacelles sur camion de 30 m ou plus (numériquement inférieurs), certaines activités, en particulier la charpenterie et l’hydraulique, se faisaient déjà en interne. Multitel Pagliero, qui à l’époque n’employait que 200 personnes, avait une approche artisanale au travail et il était difficile de trouver à l’extérieur des fournisseurs capables de réaliser une ou deux pièces à la fois, de grandes dimensions et techniquement délicates. Et de toute façon des pièces qui étaient dessinées par nous».
L’augmentation constante de la demande, avec des nombres plus élevés pour les produits de série, a été l’élément qui nous a poussés vers une réorganisation interne. «Cela a exigé des investissements en machines et en bâtiments ; en même temps, étant donné que des éléments tels que les tôles, les joints et les vannes étaient réalisés d’après nos dessins, l’opération s’en est trouvée simplifiée. Ce qui a été plus difficile a été de trouver du personnel qualifié pour utiliser les robots, les centres de travail automatiques ou les installations de peinture. Il s’agissait de notre produit, mais nous avions besoin de personnel. Ainsi nos effectifs sont-ils passés de 200 à 550 personnes». L’organisation de la chaîne logistique a donc secondé, suivi et stimulé la croissance de l’entreprise.

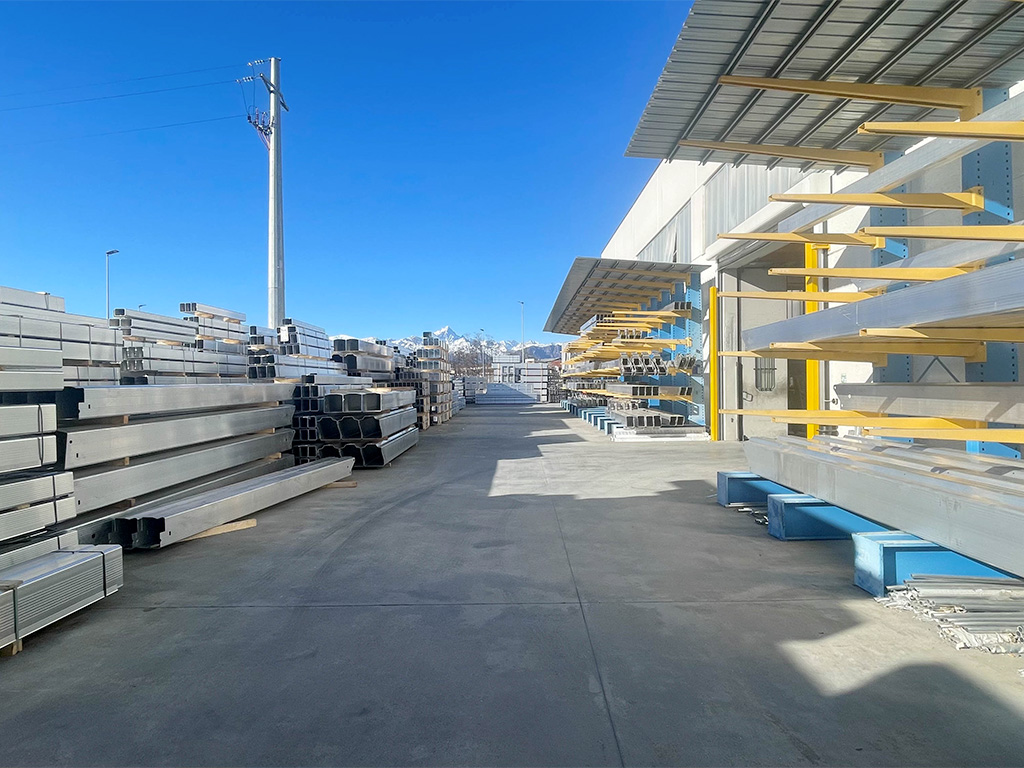
Chronologiquement, le processus d’organisation interne des travaux a comporté les phases suivantes:
2013 – aluminium (bras, paniers, contre-châssis)
2014 – achat des magasins automatiques verticaux;
2014/2015 – installation de peinture (qui était assurée à 50 % en externe) ;
2016/2018 – les cylindres, avec un gros investissement et un personnel spécialisé dans la gestion de la programmation;
2017/2018 – installations électriques;
2020 – charpenterie en fer.
En 2021, si l’activité de dessin et de conception des machines était déjà à 100 % gérée en interne, celle de la production a atteint 95 %. Les 5 % restants concernent les camions, les composants (vannes, batteries, puces électroniques, un secteur assuré par des producteurs de confiance) et la matière première (aluminium et fer). Une activité dont est responsable le bureau des achats.
«La chaîne – souligne Fabio Pagliero – fonctionne département par département, en autonomie. Bien entendu, je me confronte quotidiennement avec tous les responsables, mais il n’y a pas besoin de réunions, parce que la chaîne logistique est déjà rodée et la chaîne décisionnelle est courte. Cela permet de faire moins de stockage en magasin, de produire sur la base des commandes et cela permet aussi une meilleure qualité dans le contrôle du travail. Contrairement à un fournisseur externe, nous sommes pleinement conscients qu’il n’y a pas seulement les nacelles sur camion, il y aussi des personnes qui y montent. Et nous ne pouvons pas nous permettre de nous tromper». L’indépendance de production a imposé l’achat de machines adaptées à produire les pièces conçues par le bureau technique, chose impossible à demander un sous-traitant, qui ne travaille pas en exclusivité et qui n’a pas non plus la structure adaptée pour satisfaire la demande. «De notre côté – explique Fabio Pagliero – sachant que chaque semaine nous produisons N machines, tout est planifié. En cas de nécessité, il ne serait donc pas difficile d’ajouter une autre usine ou de réagencer la chaîne logistique et la production».
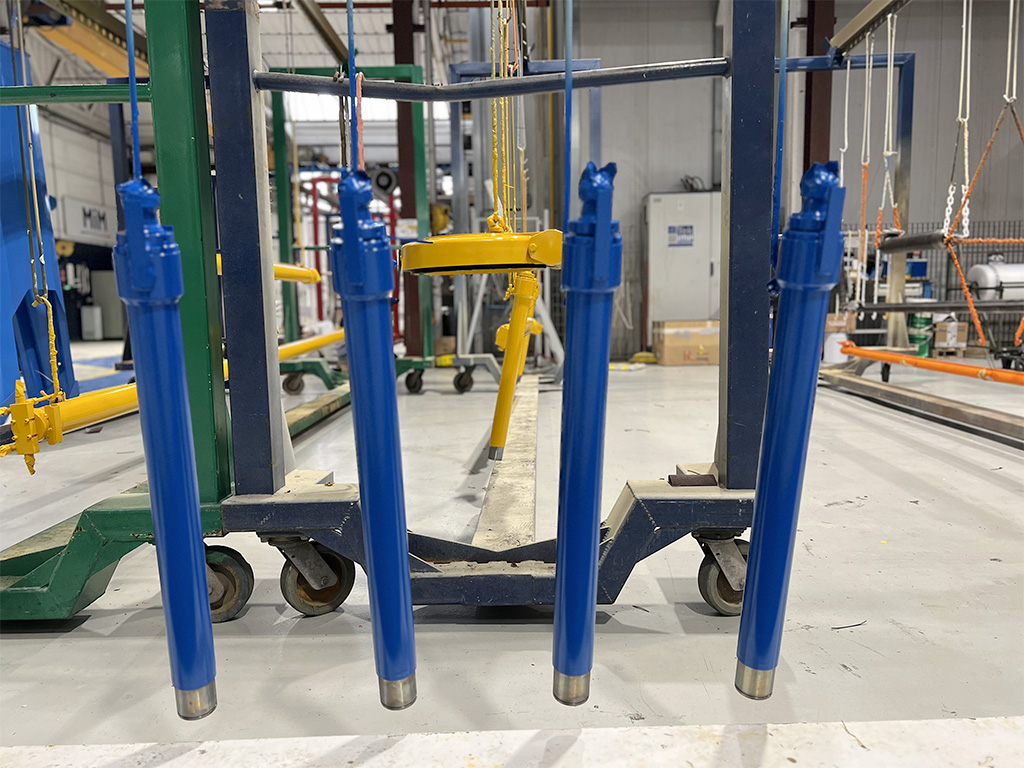
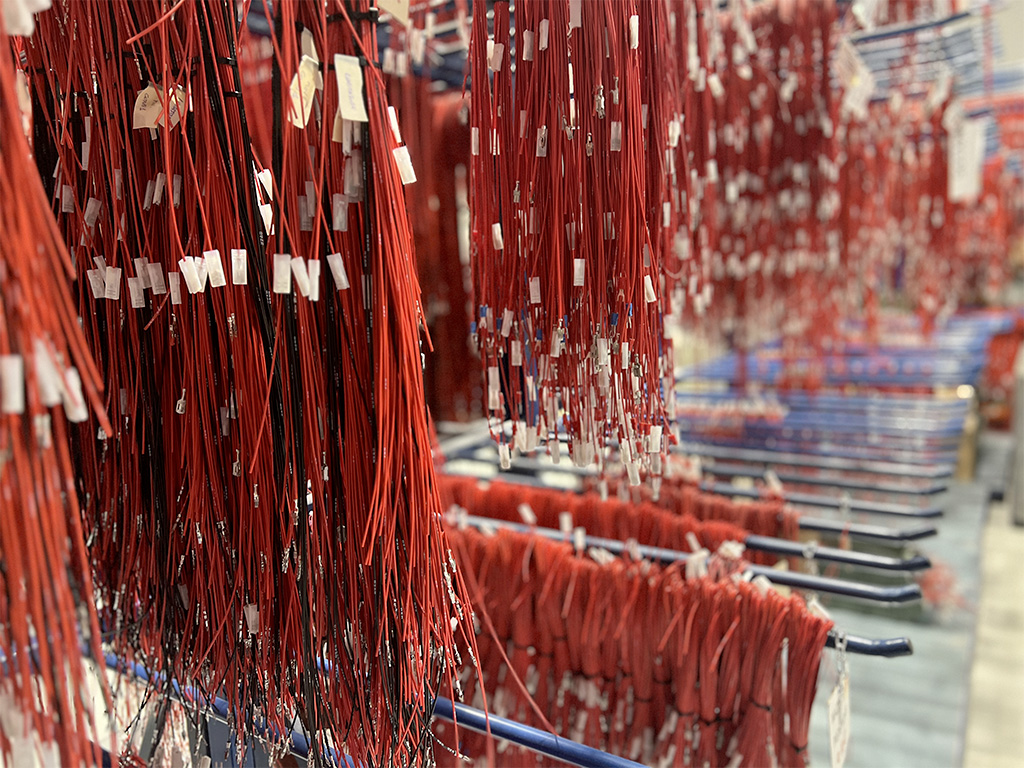
De 2021 à 2023, grâce à notre organisation, à notre structure et à notre flexibilité, nous avons pu affronter sans problème une hausse très forte de la demande, qui en 2023 a atteint un pic de 2250 unités produites, soit presque 50 machines par semaine. Il est évident que, pour gérer ce type de production, le personnel doit être très spécialisé et, comme ce genre de personnel n’est pas facile à trouver, il lui faut suivre une formation dès son entrée dans notre usine. Ceux qui ont de l’expérience, non seulement développent le patrimoine de connaissances techniques, mais le partagent avec les nouvelles ressources, de façon à créer un «langage commun». Cela est indispensable, du fait qu’il y a 8 unités autonomes à technologie élevée, avec des machines qui fonctionnent 16 heures par jour, chacune dédiée à une activité: soudage de l’aluminium, soudage du fer, travaux au tour, peinture, réalisation des tableaux électriques. Des usines qui, individuellement, sont en mesure de générer des affaires, qui travaillent sans contamination et dont sortent les éléments destinés à l’unité d’assemblage des nacelles sur camion. L’informatique, avec Industrie 4.0, a contribué de manière décisive à la gestion des données et au suivi permanent de la chaîne de production, permettant de coordonner les temps et de respecter les livraisons.
Est-il possible de faire davantage et de le faire mieux ?
«Toute activité – conclut Fabio Pagliero – peut-être améliorée, mais, en l’état, la chaîne logistique Multitel Pagliero est presque parfaite. Si nous devions transférer en interne un autre genre de travail, je dirais l’électronique, c’est-à-dire les cartes, qui représentent le projet le plus ambitieux à réaliser».